Introduction:
In the world of automation, Programmable Logic Controllers (PLCs) play a crucial role in controlling and monitoring various industrial processes. To efficiently communicate with the outside world, PLCs rely on Input and Output (I/O) modules. In this article, we will delve into the fundamentals of I/O modules in PLCs, their significance, and how they contribute to the overall functioning of the system.
1. Understanding PLCs:
Before diving into the specifics of I/O modules, it is important to grasp the basic concept of PLCs. A PLC is a robust electronic device used to automate and control industrial operations. It acts as the brain of the system, receiving input signals, processing them through the internal logic, and generating output signals accordingly.
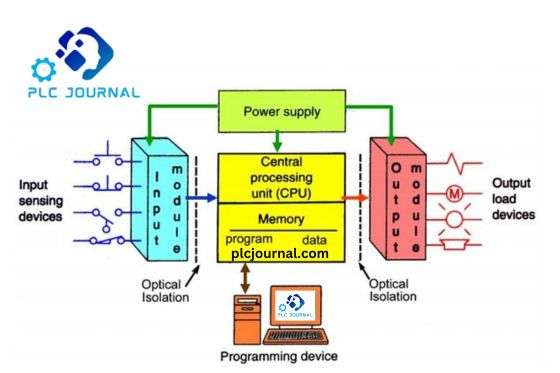
2. The Role of I/O Modules:
The I/O module acts as a bridge linking the tangible realm and the internal processing unit of the PLC. It enables communication between the external devices or sensors and the PLC itself. Simply put, the input module takes in signals from the external devices, while the output module sends signals to control different processes.
3. Input Module:
The input module, often referred to as the input card, handles the reception of signals from different sensors or devices linked to the PLC. This can include proximity sensors, switches, temperature sensors, flow meters, and more. This module translates both analog and digital signals into a format that the PLC can comprehend.
4. Functionality of Input Module:
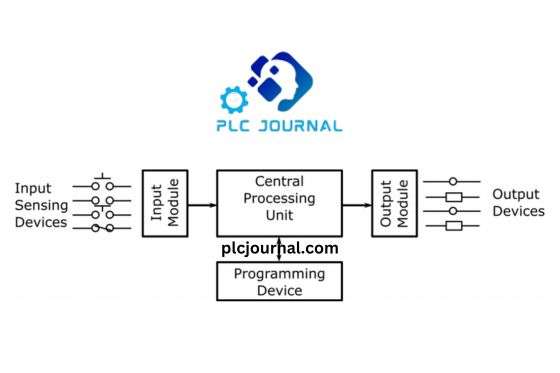
The input module scans the connected devices at regular intervals, collecting data from these devices. It then transmits this data to the central processing unit (CPU) of the PLC. The CPU then examines the states of the inputs and performs the desired logic operations based on the program instructions.
5. Output Module:
On the other hand, the output module takes the processed signals from the CPU and converts them into a form that can be utilized by the external devices, such as actuators, motors, solenoids, and valves. In essence, the output module serves as the messenger, relaying control signals from the PLC to the peripherals.
6. Key Features of Output Modules:
Output modules typically come with various features, including multiple channels that can control different devices simultaneously, relay outputs for switching higher loads, and the ability to handle different electrical current and voltage levels based on the specific requirements of the devices connected.
7. Importance of I/O Module Selection:
Selecting the appropriate I/O module for a particular application is crucial in ensuring optimal performance and reliability. Factors such as input/output compatibility, channel count, signal type, voltage rating, communication protocols, and environmental considerations need to be thoroughly evaluated and matched with the requirements of the industrial process.
8. Communication Protocols:
PLCs support various communication protocols to interact with different devices and systems. Frequently utilized protocols encompass Ethernet/IP, Modbus, Profibus, and DeviceNet. The compatibility of the I/O module with the chosen communication protocol is essential to establish seamless communication between the PLC and the external devices.
9. Expansion and Flexibility:
PLCs often require expansion modules to accommodate additional inputs and outputs as the system grows or new automation needs arise. Expansion modules can easily be added to the existing I/O architecture, enhancing the flexibility of the system.
What are the Input-Output Modes of PLC?
1. Discrete Input/Output
Discrete input/output (I/O) is one of the most common modes of PLC operation. Discrete I/O modules interface with digital devices such as sensors, switches, and actuators that have a binary state, i.e., ON or OFF. These I/O modules convert the signals received from these devices into digital data that can be processed by the PLC. Discrete I/O is typically used for applications that involve monitoring events or controlling discrete devices.
2. Analog Input/Output
Analog I/O is used when dealing with continuous data values, such as temperature, pressure, flow rate, or voltage. Analog input modules convert the incoming analog signals into digital form for the PLC to process, while analog output modules generate analog signals based on the processed data from the PLC. Through analog I/O, the PLC gains the ability to oversee and regulate variables spanning a broad spectrum of values, facilitating finer automation in industrial operations.
3. High-Speed Input/Output
High-speed I/O modules are designed to handle fast-changing signals and high-speed events. These modules are typically used in applications that require precise timing and rapid response, such as high-speed sorting, packaging, or machine control. High-speed I/O modules are capable of capturing signals in milliseconds or microseconds, providing the PLC with real-time data for accurate decision-making and control.
4. Network Communication
PLCs can also communicate with other devices or systems on a network. This mode of operation allows the PLC to exchange data with other PLCs, human-machine interfaces (HMIs), supervisory control and data acquisition (SCADA) systems, or other networked devices. Network communication enables remote monitoring, control, and data sharing, facilitating efficient collaboration and integration of multiple processes.
5. Specialty I/O
Besides the standard input-output modes, PLCs may also have specialty I/O modules to cater to specific industrial requirements. Such modules find common usage in applications necessitating precise timing and swift responsiveness, like high-speed sorting, packaging, or machine control tasks. Specialty I/O modules are tailored to handle unique input/output signals, enhancing the flexibility and functionality of PLC systems in specific automation scenarios.
Exploring the Types of Input and Output Modules
PLCs can utilize several types of Input and Output Modules. The most common are digital and analog modules.
Digital Modules
Digital input and output modules process signals that are either on or off, like switches. This means the incoming or outgoing signals hold binary values—either (off) or 1 (on).
Analog Modules
Analog input and output modules, on the other hand, interpret and send continuous signals. This capacity to read varying degrees of signal value allows PLCs to monitor and control processes like temperature, pressure, or flow rates more precisely.
Assessing Importance
The Importance of the Input and Output Module in PLCs cannot be overstated. They form the fundamental nodes of communication between the controller and peripheral devices.
Conclusion:
In conclusion, the input and output modules in PLCs play a vital role in establishing seamless communication between the PLC and external devices. The input module collects data from sensors and transmits it to the CPU, while the output module receives processed signals from the CPU and controls external devices.
The proper selection of I/O modules, based on factors like compatibility, channel count, and communication protocols, ensures optimal performance and flexibility in industrial automation processes. Understanding the importance and role of I/O modules empowers us to maximize the capabilities of PLCs, driving efficient and dependable automation solutions.
Technical Guides
What Is a Programmable Logic Controller (PLC)? Full Explanation
What is HMI? Human-Machine Interface (HMI)-Full Explanation
What is a Variable Frequency Drive?-It’s complete guidelines
What Is a Servo drive and How Does it Work? It’s complete guidelines
Manual PDF
[PDF] Delta PLC DVP-ES2/EX2/SS2/SA2/SX2/SE&TP Operation Manual Free Download
Delta HMI-DOPSoft User Manual Free Download [PDF]
Cable Making
[DIY-Cable] PLC/HMI-Panasonic Connecting PC
[DIY-Cable] PLC/HMI-Keyence Connecting PC
[DIY-Cable] S7-200 Siemens Connecting PC
[DIY-Cable] Mitsubishi PLC Programming Cable SC-09 for FX-Series
[DIY-Cable] PLC Delta Programming Cable DVPACAB230
[DIY-Cable] PLC OMRON Programing Cable for CJ/CS/CQ-Series
[DIY-Cable] PLC “LS/LG” Programing Cable
[DIY-Cable] PLC “Fatek/Facon” Programing Cable
[DIY-Cable] PLC “Vigor” Programing Cable
[DIY-Cable] HMI “Fuji/Hakko” Programing Cable
[DIY-Cable] “HMI Omron NT-Series” Programing Cable
[DIY-Cable] HMI Keyence “VT3-W4 Series” Cable Connecting To PLC
[PDF] HMI-Weintek Connection PLC Guide