Introduction:
Programmable Logic Controllers (PLCs) are indispensable tools used in industrial automation to control and monitor machinery and processes. PLC programming languages are a crucial aspect of this automation process, as they determine how the controller interacts with the machinery or devices it controls. In this article, we will delve into the top 5 PLC programming languages widely used in the industry today.
1. Ladder Logic (LAD):
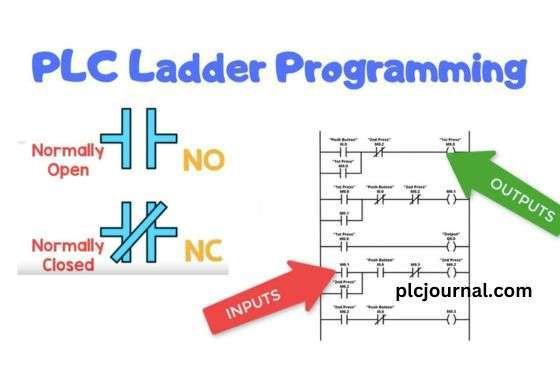
Ladder Logic, also known as LAD, is one of the most commonly used PLC programming languages. It derives its name from the ladder-like appearance of the programming diagrams. LAD mimics the behavior of electromechanical relays, making it intuitive for electricians or technicians familiar with traditional relay circuits. The visual representation of circuits in Ladder Logic allows for easy troubleshooting and modification.
2. Structured Text (ST):

Structured Text (ST) is a high-level PLC programming language resembling the syntax of the Pascal programming language. It offers a wide range of programming possibilities, making it suitable for complex control algorithms or mathematical operations. ST is mainly used for implementing advanced control strategies and mathematical calculations within PLC programs. However, its usage requires a solid understanding of programming concepts.
3. Function Block Diagram (FBD):
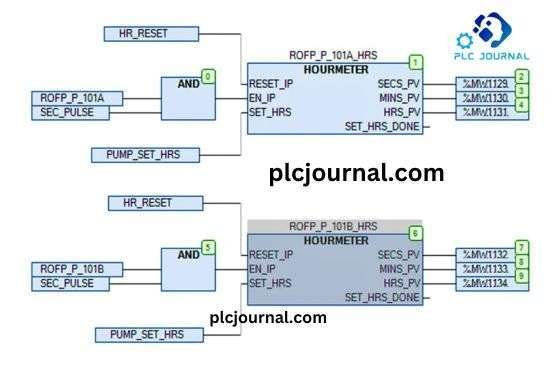
Function Block Diagram (FBD) is a graphical programming language that utilizes interconnected function blocks to represent the control logic. Each block represents a specific function, and the interconnections between blocks dictate the sequence of operations. FBD is a versatile language that allows for modular programming, making it easy to reuse and maintain code. It is particularly useful for designing complex control systems involving multiple devices or machines.
4. Instruction List (IL):
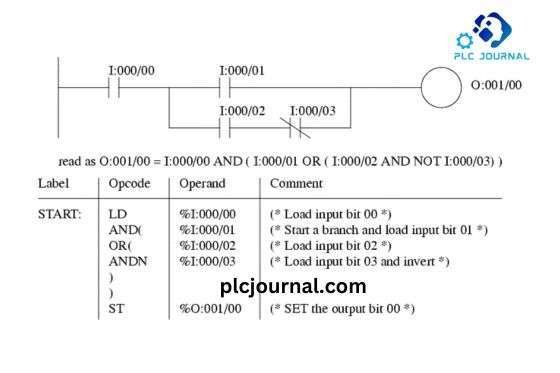
Instruction List (IL) is a low-level PLC programming language mainly used by experienced programmers. It resembles assembly language and requires a good understanding of the PLC’s instruction set. IL is concise and efficient, making it ideal for time-critical applications. However, due to its complexity, it is less commonly utilized compared to other languages.
5. Sequential Function Chart (SFC):
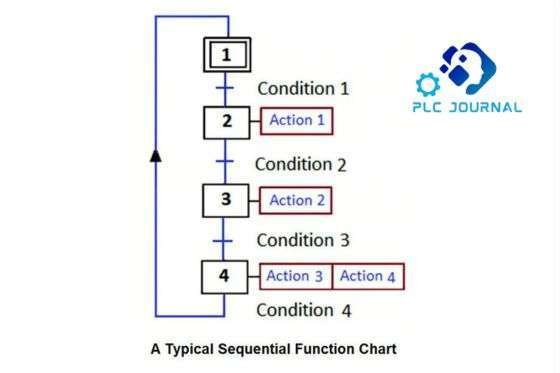
Sequential Function Chart (SFC) is a graphical PLC programming language used to model complex control sequences. It allows representing the sequential flow of operations using steps, transitions, and actions. SFC is particularly effective in applications where a machine or process undergoes sequential steps, such as batch processing. The visual representation facilitates the analysis and understanding of the control flow.
Which Language is Best for PLC
Understanding PLC Programming Languages
PLC programming languages are specific to the manufacturer’s hardware and software. The most common programming languages used for PLCs are ladder logic, structured text, function block diagram, and instruction list.
Ladder Logic – The Traditional Standard
Ladder Logic, also known as relay logic, is a graphical programming language that resembles electrical circuit diagrams. Its visual representation makes it easy for electricians and technicians to understand. Ladder Logic is best suited for simple and sequential control processes.
Structured Text – The Versatile Option
Structured Text is a high-level programming language similar to Pascal or C. It allows programmers to write complex algorithms and perform mathematical calculations easily. Structured Text is ideal for applications that require advanced mathematical operations, data manipulation, and complex control structures.
Function Block Diagram – Modular Approach
Function Block Diagram (FBD) is a graphical programming language that utilizes functional blocks interconnected with wires. Each function block represents specific logic or operation. FBD is beneficial for modular programming as it allows reusability and enhances the readability of complex programs.
Instruction List – Low-Level Programming
Instruction List (IL) is a low-level programming language that works with simple instructions executed sequentially. IL resembles assembly language and is typically used for specific tasks requiring precise timing and performance optimization.
Factors to Consider in PLC Programming Language Selection
Now that you are aware of the different programming languages, it is essential to consider various factors before deciding the best language for your PLC project.
Complexity and Functionality
Evaluate the complexity and functionality of your automation process. If the operation is simple and sequential, ladder logic might be the suitable choice. However, for complex algorithms and mathematical calculations, structured text provides more flexibility.
Programmer’s Expertise
Consider the expertise and proficiency of your programming team. If you have experienced programmers familiar with certain languages, using those languages can facilitate faster development and easier maintenance.
Performance and Efficiency
Different programming languages have varying performance capabilities. If your application requires precise timing and optimal speed, low-level languages like instruction list could be the preferred option.
Hardware and Software Compatibility
Ensure that the selected programming language is compatible with your PLC hardware and software. Some PLCs might only support specific languages, and choosing the wrong language can result in compatibility issues.
What is the basic programming language for PLC?
Understanding the Basics
The basic programming language for PLCs is known as Ladder Logic. Ladder Logic, often referred to as “Ladder Diagram,” is a graphical representation of the control logic used to program PLCs. It takes its name from the ladder-like appearance of the program, which resembles a series of rungs on a ladder.
Ladder Logic was developed to be easily understood by electricians and technicians who were already familiar with relay-based control systems. In essence, it provides a visual and intuitive way to create control sequences, making it accessible to a wide range of professionals.
The Components of Ladder Logic
Ladder Logic consists of various components, each serving a specific function within the program. These components include:
1. Contacts (Input Conditions):
Contacts represent the conditions that need to be met for a particular action to occur. They can be either normally open (NO) or normally closed (NC) and act as binary switches, symbolizing the status of sensors, switches, or other input devices.
2. Coils (Output Actions):
Coils represent the actions or outputs that are activated when the conditions set by the contacts are met. They control devices such as motors, solenoids, valves, and other output components.
3. Rungs:
A rung is a horizontal line in the ladder diagram that contains a combination of contacts and coils. Each rung represents a specific control sequence or operation within the program.
4. Power Rails:
Power rails, typically located on the left and right sides of the ladder diagram, provide electrical power to the contacts and coils. The left rail is for the positive voltage, while the right rail is for the neutral or ground.
5. Control Relays and Timers:
Ladder Logic can also incorporate control relays and timers, enabling more complex and time-based operations. These elements expand the capabilities of the language for handling a wide range of applications.
Writing Ladder Logic Programs
To write a Ladder Logic program, one uses a specialized software tool provided by the PLC manufacturer. This software offers a graphical interface for creating, editing, and simulating ladder diagrams. The process of programming in Ladder Logic typically involves the following steps:
Identifying the input conditions (contacts) and output actions (coils) required for the control sequence.
Creating rungs to represent the control logic. Each rung is a unique sequence in the program.
Dragging and dropping contacts and coils onto the rungs, establishing the logical relationships between them.
Defining control relay or timer instructions if needed to add complexity to the program.
Verifying the program’s functionality through simulation, ensuring that the desired outcomes are achieved.
Uploading the completed program to the PLC for execution and monitoring.
Advantages of Ladder Logic
Ladder Logic remains the preferred programming language for PLCs for several reasons:
1. Easy to Understand:
Its graphical nature makes it highly intuitive and accessible to individuals with a background in electrical and control systems.
2. Safety:
Ladder Logic emphasizes safety by its design, ensuring that control sequences are clear and reliable.
3. Versatility:
It can handle a wide range of control tasks, from simple on/off operations to complex processes involving timers, counters, and data manipulation.
4. Widely Supported:
Most PLC manufacturers support Ladder Logic, making it a universal choice across the industry.
Conclusion:
PLC programming languages play a vital role in the efficient functioning of industrial automation systems. The top 5 PLC programming languages, namely Ladder Logic (LAD), Structured Text (ST), Function Block Diagram (FBD), Instruction List (IL), and Sequential Function Chart (SFC), offer a wide range of options to implement various control strategies.
Each language has its strengths and areas of applicability, allowing programmers to choose the most suitable one based on the complexity and requirements of the automation task at hand. By understanding these programming languages and utilizing them effectively, programmers can develop robust and efficient PLC programs that drive industrial automation to new levels of productivity.
Technical Guides
What Is a Programmable Logic Controller (PLC)? Full Explanation
What is HMI? Human-Machine Interface (HMI)-Full Explanation
What is a Variable Frequency Drive?-It’s complete guidelines
What Is a Servo drive and How Does it Work? It’s complete guidelines
Manual PDF
[PDF] Delta PLC DVP-ES2/EX2/SS2/SA2/SX2/SE&TP Operation Manual Free Download
Delta HMI-DOPSoft User Manual Free Download [PDF]
Cable Making
[DIY-Cable] PLC/HMI-Panasonic Connecting PC
[DIY-Cable] PLC/HMI-Keyence Connecting PC
[DIY-Cable] S7-200 Siemens Connecting PC
[DIY-Cable] Mitsubishi PLC Programming Cable SC-09 for FX-Series
[DIY-Cable] PLC Delta Programming Cable DVPACAB230
[DIY-Cable] PLC OMRON Programing Cable for CJ/CS/CQ-Series
[DIY-Cable] PLC “LS/LG” Programing Cable
[DIY-Cable] PLC “Fatek/Facon” Programing Cable
[DIY-Cable] PLC “Vigor” Programing Cable
[DIY-Cable] HMI “Fuji/Hakko” Programing Cable
[DIY-Cable] “HMI Omron NT-Series” Programing Cable
[DIY-Cable] HMI Keyence “VT3-W4 Series” Cable Connecting To PLC
[PDF] HMI-Weintek Connection PLC Guide