Introduction:
In modern industrial settings, the Variable Frequency Drive (VFD) has become a crucial component in controlling and regulating electric motors. Understanding its fundamental components is essential to grasp its functionality and significance.
1. Overview of a VFD:
Briefly explain what a VFD is, its role in regulating motor speed, and its significance in various industries like manufacturing, HVAC systems, and more.
2. Main Components of a VFD:
a. Rectifier:
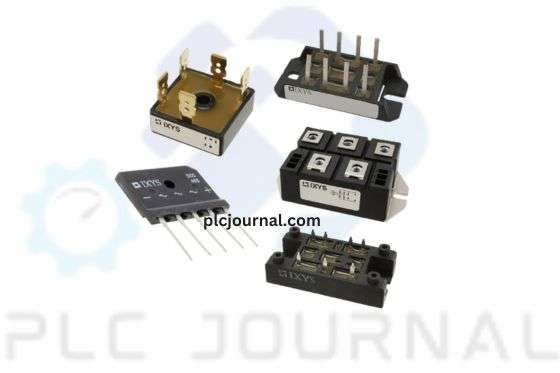
Define the rectifier and its role in converting AC power to DC power.
Explain how it ensures a stable DC power supply for the VFD.
b. DC Bus:
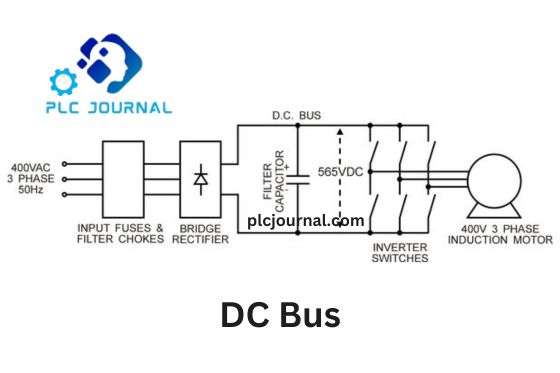
Detail the DC bus as the central link between the rectifier and the inverter.
Explain its function in storing and supplying DC power to the inverter.
c. Inverter:
Describe the inverter’s role in converting DC power back to AC power.
Explain how it manipulates the frequency and voltage to control motor speed.
d. Control Unit:
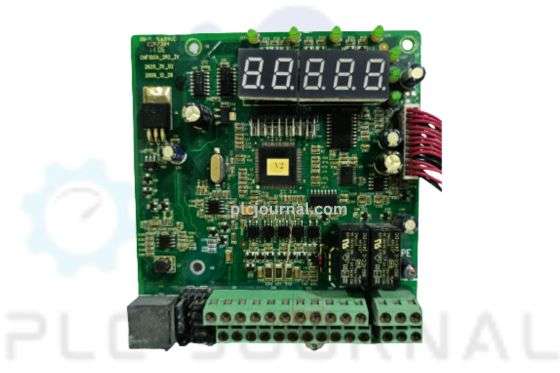
Discuss the control unit’s significance in monitoring and regulating the VFD operation.
Explain how it adjusts frequency, voltage, and other parameters for optimal motor performance.
e. Heat Sink and Cooling System:
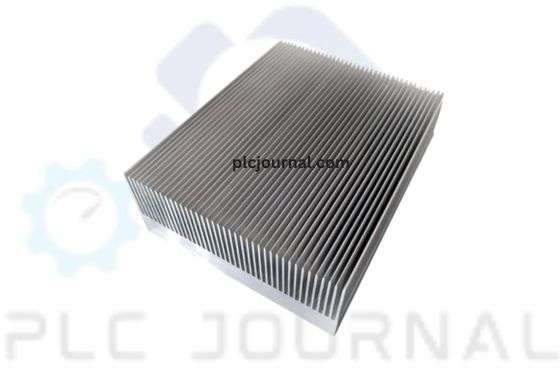
Highlight the importance of heat dissipation in a VFD.
Discuss the role of heat sinks and cooling systems in maintaining optimal operating temperatures.
f. Protective Devices:
Discuss various protective components like fuses, circuit breakers, and overload relays.
Explain their role in safeguarding the VFD and connected equipment from electrical faults.
3. Importance and Applications:
Elaborate on the significance of each component in ensuring the efficiency and functionality of the VFD.
Discuss how VFDs are used in different industries and their impact on energy savings and equipment longevity.
4. Future Trends and Innovations:
Briefly touch on emerging technologies or advancements in VFD components.
Discuss potential improvements that could enhance VFD efficiency or functionality.
What are the three main components of a VSD?
A Variable Speed Drive (VSD), also known as a Variable Frequency Drive (VFD), typically comprises three primary components:
Rectifier: This component is responsible for converting incoming AC power from the mains supply into DC power. It uses diodes to perform this conversion, ensuring a consistent and smooth flow of DC power to the subsequent components within the drive.
Inverter: The DC power generated by the rectifier is then directed to the inverter. This crucial component converts the DC power back into AC power but with adjustable frequency and voltage. By controlling the frequency and voltage, the inverter allows precise regulation of the motor’s speed and torque, offering the flexibility to cater to varying operational requirements.
Control Unit: Often considered the brain of the VSD, the control unit consists of a microprocessor or controller that manages and regulates the entire operation of the drive. It receives input signals, monitors the motor’s performance, and adjusts the output frequency and voltage accordingly. The control unit ensures optimal motor performance, efficiency, and protection by managing various parameters within the drive.
These three components work in conjunction to regulate the speed, torque, and overall performance of the connected motor, offering flexibility and efficiency in various industrial and commercial applications.
What are the basic functions of a VFD?
A Variable Frequency Drive (VFD) performs several crucial functions in controlling the operation of an electric motor. Some of the basic functions include:
Speed Control: One of the primary functions of a VFD is to regulate the speed of an electric motor. By adjusting the frequency and voltage of the electrical input, the VFD can vary the motor’s speed across a wide range, allowing precise control based on operational requirements.
Torque Control: VFDs enable precise control over the torque delivered by the motor. They can adjust the output torque according to the load demand, ensuring the motor provides the required amount of force without unnecessary power consumption.
Energy Savings: VFDs are known for their ability to save energy. By controlling the motor speed based on the actual demand of the system rather than running constantly at full speed, VFDs help reduce energy consumption, leading to significant cost savings over time.
Soft Start and Stop: VFDs facilitate smooth and gradual starts and stops of the motor, reducing mechanical stress on the equipment. This feature prolongs the motor’s lifespan and minimizes wear and tear, especially in applications where abrupt starts and stops could damage the machinery.
Process Control: In industrial settings, VFDs contribute to precise process control. They allow for adjustments in motor speed and torque, ensuring that machinery operates at optimal levels, meeting production requirements efficiently.
Protection and Monitoring: VFDs come equipped with various protective features such as overload protection, overvoltage and undervoltage protection, short circuit protection, and thermal protection. They also offer monitoring capabilities to track motor performance and detect any anomalies, ensuring the system’s safety and longevity.
Compatibility and Adaptability: VFDs are adaptable to various motor types and sizes, making them versatile for different applications. They can accommodate changes in load demands and adjust accordingly, offering flexibility in diverse industrial and commercial environments.
Understanding these fundamental functions helps in appreciating the significance of VFDs in optimizing motor performance, energy efficiency, and system reliability across a wide range of applications.
Conclusion:
Summarize the importance of understanding the components of a VFD for its efficient operation and its role in modern industrial applications.
Technical Guides
What Is a Programmable Logic Controller (PLC)? Full Explanation
What is HMI? Human-Machine Interface (HMI)-Full Explanation
What is a Variable Frequency Drive?-It’s complete guidelines
What Is a Servo drive and How Does it Work? It’s complete guidelines
Manual PDF
[PDF] Delta PLC DVP-ES2/EX2/SS2/SA2/SX2/SE&TP Operation Manual Free Download
Delta HMI-DOPSoft User Manual Free Download [PDF]
Cable Making
[DIY-Cable] PLC/HMI-Panasonic Connecting PC
[DIY-Cable] PLC/HMI-Keyence Connecting PC
[DIY-Cable] S7-200 Siemens Connecting PC
[DIY-Cable] Mitsubishi PLC Programming Cable SC-09 for FX-Series
[DIY-Cable] PLC Delta Programming Cable DVPACAB230
[DIY-Cable] PLC OMRON Programing Cable for CJ/CS/CQ-Series
[DIY-Cable] PLC “LS/LG” Programing Cable
[DIY-Cable] PLC “Fatek/Facon” Programing Cable
[DIY-Cable] PLC “Vigor” Programing Cable
[DIY-Cable] HMI “Fuji/Hakko” Programing Cable
[DIY-Cable] “HMI Omron NT-Series” Programing Cable
[DIY-Cable] HMI Keyence “VT3-W4 Series” Cable Connecting To PLC
[PDF] HMI-Weintek Connection PLC Guide