What Is a Programmable Logic Controller (PLC)?
In today’s fast-paced industrial landscape, automation plays a pivotal role in streamlining processes, enhancing efficiency, and reducing human intervention. Programmable Logic Controllers (PLCs) are the unsung heroes behind this automation revolution. In this comprehensive guide, we will dive deep into the world of PLCs, exploring their types, programming methods, advantages, and how they work. So, let’s embark on a journey to unravel the secrets of Programmable Logic Controllers.
Introduction
Programmable Logic Controllers, often abbreviated as PLCs, are specialized digital computers designed for industrial automation and control systems. They are the brains behind a wide range of automated processes, from manufacturing assembly lines to energy management systems. PLCs are designed to withstand the harsh conditions of industrial environments, making them a reliable choice for mission-critical operations.
What are the 3 Types of PLC?
PLCs can be classified into three categories based on their processing power and complexity:
1. Low-End PLC
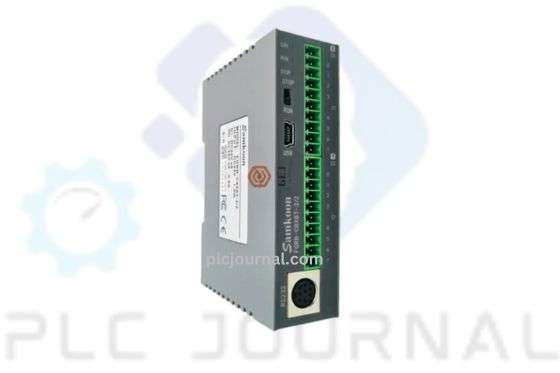
Low-end PLCs are suitable for basic control tasks and have limited processing capabilities.
2. Mid-Range PLC
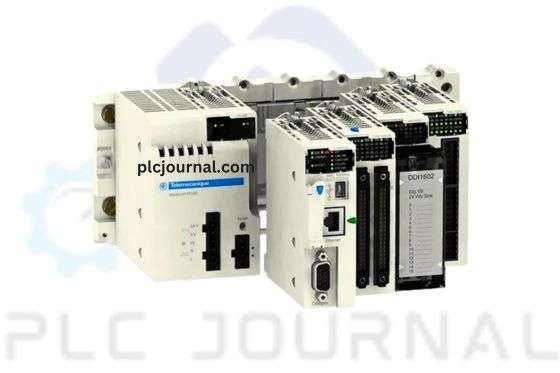
Mid-range PLCs offer more processing power and memory, making them suitable for a wide range of applications.
3. High-End PLC
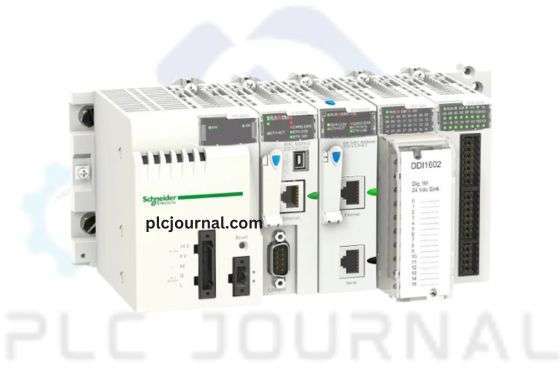
High-end PLCs are equipped with advanced features, including redundancy and extensive communication options. They are ideal for complex and mission-critical applications.
What are the Different Types of PLC?
PLCs come in various types and sizes, each catering to specific industrial needs. Let’s take a look at some typical types of PLCs:
1. Modular PLC
Modular PLCs allow for the customization of input and output options. They consist of separate modules that can be added or removed as needed, providing flexibility in system design.
2. Compact PLC
Compact PLCs are smaller in size and are ideal for applications with limited space. They are cost-effective and offer basic automation capabilities.
3. Rack-Mountable PLC
Rack-mountable PLCs are designed to be installed in standard equipment racks. They are commonly used in large-scale industrial systems.
4. Safety PLC
Safety PLCs prioritize safety-critical functions. They are equipped with advanced features like redundancy and self-diagnostics to ensure the protection of workers and assets.
How is a PLC Programmed?
Programming a PLC involves creating a set of instructions that dictate how it should operate. PLCs use ladder logic, a graphical programming language that resembles electrical relay logic diagrams. Programmers can also use text-based programming languages such as Structured Text (ST) and Function Block Diagram (FBD). PLC programming requires a deep understanding of the specific industrial process it will control.
Advantages of Using PLC
Utilizing PLCs in industrial automation offers several advantages:
– Reliability
PLCs are known for their robustness and reliability, ensuring consistent performance even in harsh conditions.
– Flexibility
They can be easily reprogrammed to adapt to changing manufacturing requirements, reducing downtime during transitions.
– Cost-Efficiency
PLCs are cost-effective solutions for automating various processes, making them suitable for both small and large-scale industries.
– Diagnostics
PLCs provide real-time diagnostics, making it easier to identify and troubleshoot issues, minimizing production disruptions.
How a Programmable Logic Controller Works
PLCs work by continuously monitoring input devices such as sensors and switches. Based on predefined logic and algorithms, they make decisions and control output devices like motors, valves, and actuators. This cycle repeats in real-time, ensuring precise and consistent control over industrial processes
Choosing a PLC
Selecting the right PLC for your application is crucial. Consider factors such as the complexity of your automation process, environmental conditions, and budget constraints. Consulting with automation experts can help you make an informed decision.
Enclosures for Protecting Your PLC
PLCs are often exposed to dust, moisture, and extreme temperatures in industrial settings. To ensure their longevity and performance, it’s essential to install them in suitable enclosures. Enclosures protect PLCs from environmental hazards and mechanical damage.
Conclusion
In conclusion, Programmable Logic Controllers are indispensable tools in the world of industrial automation. They offer reliability, flexibility, and efficiency, making them vital components in various industries. Understanding the different types of PLCs, their programming methods, and their advantages is essential for harnessing their full potential in automation projects.
(Frequently Asked Questions): What Is a Programmable Logic Controller (PLC)?
PLC stands for Programmable Logic Controller, a device used to control and automate various industrial processes.
PLC, or Programmable Logic Controller, operates by monitoring input devices, making decisions based on predefined logic, and controlling output devices to automate industrial processes.
A PLC, or Programmable Logic Controller, could be used to control the operation of an assembly line in a manufacturing plant, ensuring products are produced with precision and efficiency.
PLCs are used in industrial settings to improve efficiency, reliability, and control over processes, ultimately reducing human intervention and errors.
PLC (Programmable Logic Controller) and SCADA (Supervisory Control and Data Acquisition) are complementary systems. PLCs control machinery and processes, while SCADA systems collect and visualize data for monitoring and control in real-time.
Technical Guides
What Is a Programmable Logic Controller (PLC)? Full Explanation
What is HMI? Human-Machine Interface (HMI)-Full Explanation
What is a Variable Frequency Drive?-It’s complete guidelines
What Is a Servo drive and How Does it Work? It’s complete guidelines
Manual PDF
[PDF] Delta PLC DVP-ES2/EX2/SS2/SA2/SX2/SE&TP Operation Manual Free Download
Delta HMI-DOPSoft User Manual Free Download [PDF]
Cable Making
[DIY-Cable] PLC/HMI-Panasonic Connecting PC
[DIY-Cable] PLC/HMI-Keyence Connecting PC
[DIY-Cable] S7-200 Siemens Connecting PC
[DIY-Cable] Mitsubishi PLC Programming Cable SC-09 for FX-Series
[DIY-Cable] PLC Delta Programming Cable DVPACAB230
[DIY-Cable] PLC OMRON Programing Cable for CJ/CS/CQ-Series
[DIY-Cable] PLC “LS/LG” Programing Cable
[DIY-Cable] PLC “Fatek/Facon” Programing Cable
[DIY-Cable] PLC “Vigor” Programing Cable
[DIY-Cable] HMI “Fuji/Hakko” Programing Cable
[DIY-Cable] “HMI Omron NT-Series” Programing Cable
[DIY-Cable] HMI Keyence “VT3-W4 Series” Cable Connecting To PLC
[PDF] HMI-Weintek Connection PLC Guide
This website is a treasure trove of information! I love how user-friendly it is, making navigation a breeze. Keep up the fantastic work.