Introduction
In the realm of motor control, the choices between Servo Drives and Stepper Drives play a pivotal role in determining precision, performance, and suitability for diverse applications. Understanding the nuances between these two drive types is crucial for making informed decisions in the industrial landscape.
Defining Servo Drives and Stepper Drives
Servo Drives:
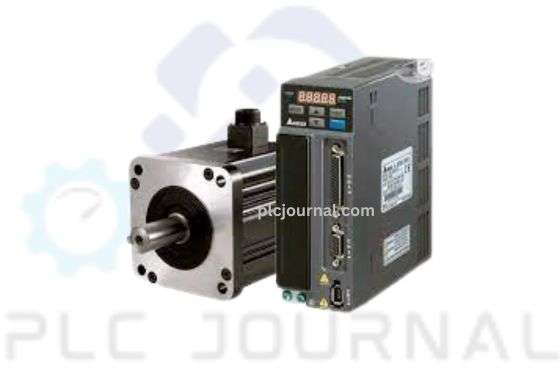
Elaborate on Servo Drives, emphasizing their role in controlling high-performance motors with precision and accuracy. Highlight their closed-loop control mechanism, feedback systems, and suitability for dynamic applications requiring speed, torque, and position control.
Stepper Drives:
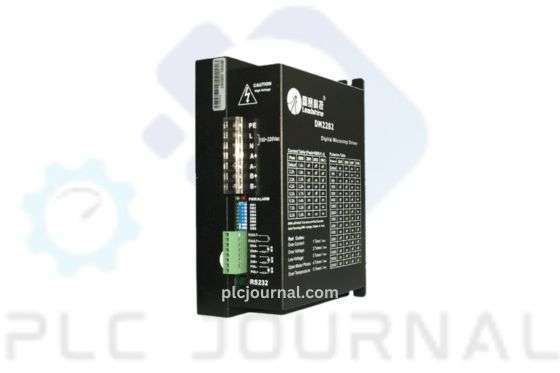
Detail Stepper Drives, showcasing their open-loop control system and ability to move in discrete steps. Discuss their simplicity, cost-effectiveness, and suitability for applications where precise positioning is crucial.
Differences in Working Principles
Control Mechanism:
Explain the primary distinction lies in control mechanisms – Servo Drives employ closed-loop control using feedback from encoders or sensors for accurate positioning, while Stepper Drives utilize open-loop control, moving in predetermined steps without feedback.
Precision and Accuracy:
Highlight the superior precision and accuracy of Servo Drives due to their closed-loop nature, compared to the inherent step resolution of Stepper Drives that can lead to positional errors.
Torque and Speed:
Discuss how Servo Drives offer high torque at high speeds, adapting dynamically to changing load conditions, whereas Stepper Drives may experience reduced torque at higher speeds due to their design limitations.
Applications and Suitability
Industrial Applications:
Explore industries where Servo Drives excel, such as CNC machining, robotics, and high-speed automation, due to their ability to handle complex tasks with precision.
Discuss Stepper Drives’ suitability in simpler applications like 3D printers, CNC routers, and small-scale automation, where cost-effectiveness and simplicity are key.
Dynamic Versus Static Applications:
Emphasize Servo Drives’ adaptability to dynamic and demanding environments requiring rapid changes in speed and position, contrasting with Stepper Drives’ effectiveness in static applications where precise positioning is paramount.
Cost and Complexity Considerations
Cost Analysis:
Discuss the cost implications – Servo Drives tend to be more expensive due to their higher precision and performance capabilities, while Stepper Drives offer a cost-effective solution for simpler applications.
Complexity and Setup:
Highlight the complexity in configuring Servo Drives with feedback systems and tuning parameters compared to the relative simplicity of setting up Stepper Drives.
What is the difference between stepper and servo power?
The difference between stepper and servo power lies in how these systems operate and control the motors they drive.
Stepper Power:
Characteristics: Stepper motors are generally used with open-loop control systems. They operate by receiving a sequence of digital pulses that dictate the movement in discrete steps.
Power Control: Stepper power is typically characterized by its ability to produce a relatively constant level of torque across a wide range of speeds, although this torque may decrease at higher speeds.
Usage: Stepper motors are commonly used in applications that require precise positioning but don’t necessarily require high speeds or dynamic performance. They are well-suited for applications where cost-effectiveness and simplicity are essential, such as in 3D printers, CNC routers, and small-scale automation.
Servo Power:
Characteristics: Servo motors are part of closed-loop control systems, which means they incorporate feedback mechanisms (like encoders) that constantly provide information about the motor’s position, allowing for precise control over speed, torque, and position.
Power Control: Servo power is known for its high performance, offering dynamic and precise control over speed and torque. Servo motors can maintain high torque at high speeds, making them suitable for applications that demand high performance and adaptability to changing load conditions.
Usage: Servo systems excel in applications that require high-speed and high-precision movements, such as in CNC machining, robotics, and high-speed automation, where accuracy, speed, and adaptability are crucial.
Difference in Power:
The key difference in power between stepper and servo systems lies in their control mechanisms and performance characteristics. Stepper power maintains relatively constant torque across a range of speeds but may lack dynamic responsiveness. In contrast, servo power offers high torque at high speeds and is capable of dynamically adapting to varying load conditions, providing superior performance and precision.
Understanding these differences helps in choosing the right system based on specific application requirements, balancing factors like precision, speed, adaptability, and cost-effectiveness.
What is the difference between a servo drive and a motor?
The distinction between a servo drive and a motor lies in their functionalities and roles within a motion control system:
Servo Motor:
Function: A servo motor is an electromechanical device that converts electrical energy into mechanical energy to create motion.
Characteristics: Servo motors are designed for high precision, accuracy, and dynamic performance. They provide precise control over speed, torque, and position in response to signals received from a control system.
Construction: Servo motors often incorporate feedback devices, such as encoders or resolvers, to provide information about the motor’s position and speed. This feedback enables closed-loop control systems to ensure accurate positioning and movement.
Servo Drive:
Function: A servo drive, also known as a servo amplifier or servo controller, is an electronic device responsible for powering, controlling, and regulating the operation of a servo motor.
Characteristics: The servo drive receives signals from a control system and amplifies them to control the motor’s speed, torque, and position. It provides the necessary power and voltage to the motor based on the control signals it receives.
Control Signals: The servo drive interprets control signals, often in the form of pulses or analog voltage, and converts them into appropriate electrical currents and voltages to drive the servo motor.
Feedback Processing: In closed-loop systems, the servo drive processes feedback from sensors like encoders to ensure the motor operates according to the desired parameters set by the control system.
Difference:
The fundamental difference between a servo motor and a servo drive is their functionality within a motion control system. The servo motor is the mechanical component responsible for converting electrical energy into motion, while the servo drive is the electronic component that powers, controls, and regulates the motor’s operation by interpreting control signals and feedback.
In summary, the servo motor is the mechanical actuator that generates motion, while the servo drive is the electronic device that controls and powers the motor to achieve the desired movement, precision, and performance in various industrial and automation applications.
Conclusion
In conclusion, recognizing the differences between Servo Drives and Stepper Drives delineates their unique strengths and applications. While Servo Drives excel in precision and adaptability for dynamic tasks, Stepper Drives offer simplicity and cost-effectiveness for applications prioritizing precise positioning. Understanding these distinctions is pivotal for optimal motor control in varied industrial and commercial settings.
Technical Guides
What Is a Programmable Logic Controller (PLC)? Full Explanation
What is HMI? Human-Machine Interface (HMI)-Full Explanation
What is a Variable Frequency Drive?-It’s complete guidelines
What Is a Servo drive and How Does it Work? It’s complete guidelines
Manual PDF
[PDF] Delta PLC DVP-ES2/EX2/SS2/SA2/SX2/SE&TP Operation Manual Free Download
Delta HMI-DOPSoft User Manual Free Download [PDF]
Cable Making
[DIY-Cable] PLC/HMI-Panasonic Connecting PC
[DIY-Cable] PLC/HMI-Keyence Connecting PC
[DIY-Cable] S7-200 Siemens Connecting PC
[DIY-Cable] Mitsubishi PLC Programming Cable SC-09 for FX-Series
[DIY-Cable] PLC Delta Programming Cable DVPACAB230
[DIY-Cable] PLC OMRON Programing Cable for CJ/CS/CQ-Series
[DIY-Cable] PLC “LS/LG” Programing Cable
[DIY-Cable] PLC “Fatek/Facon” Programing Cable
[DIY-Cable] PLC “Vigor” Programing Cable
[DIY-Cable] HMI “Fuji/Hakko” Programing Cable
[DIY-Cable] “HMI Omron NT-Series” Programing Cable
[DIY-Cable] HMI Keyence “VT3-W4 Series” Cable Connecting To PLC
[PDF] HMI-Weintek Connection PLC Guide
This website is a breath of fresh air! The clean layout and easy navigation make it a pleasure to explore. I’m impressed with the high-quality content and attention to detail.